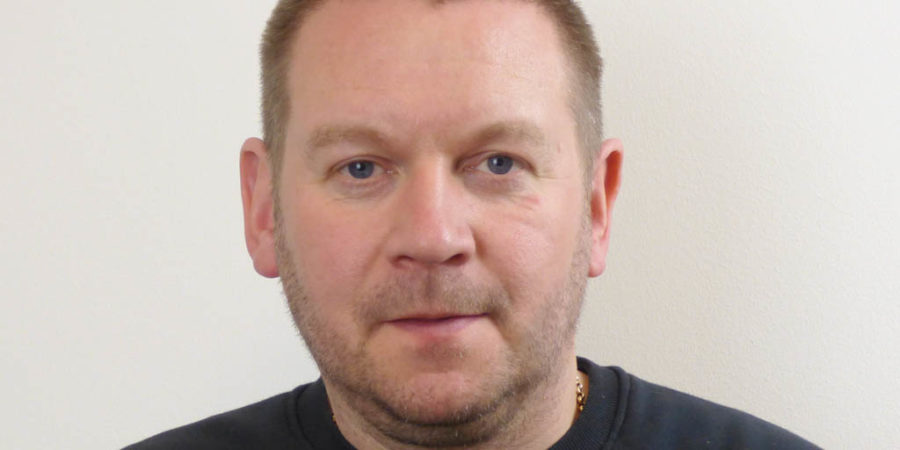
Over the coming weeks on the blog, we will get to know some of the key team members here at Advanced Composites. Today, in the first in our series of profiles – we meet with our head of Production – Tony Wilson
Hey Tony how are you doing?
I’m great thanks – as you might expect its a very busy time right now as our new manufacturing facility gets up to speed so I’ve been extremely busy this last few weeks!
And what kind of things have you been working on lately?
Well my role here at Advanced Composites is the Director of Manufacturing so literally everything that happens on the workshop floor is accountable to me. We have hundreds of different types of mandrills to create all sorts of different composite tubes and components for our clients, in addition to the actual manufacture of the components we then offer virtually unlimited options for finishing, reinforcing or painting these components as well so there are always many different processes and jobs happening all at the same time.
And it sounds like you’re only going to be getting busier?
Yes I’d say so – at the moment as things gear up we still have some areas of the factory that are being setup and configured for future work and the like so yes as more areas of the factory come online shortly then I’m sure its going to be getting even busier
And before starting Advanced Composites what kind of projects have you been working on?
Well over the years its quite a list – some of the names will be very well known; companies like Dyson or Subaru would be the obvious ones but honestly there has been a really long list over the years – Airbus, Thales, Racal, Stryker, Renishaw, Space Vac, Formula one, Cobham, Qinetic, Racal, Flight Refuelling, Gill Instruments, Premier drums, Edwards Vacuum, DERA, Eschmann… Its the great thing about Composites is that these materials have unbelievable qualities but they can be used in so many different areas.
That sounds like quite a varied CV?
It’s just the nature of the beast really – composites are very flexible so we are always working in new and interesting areas.
A material like Kevlar is a great example – everyone has heard of Kevlar being used as the material that bullet proof vests and personal protection is made out of… but the same properties that make Kevlar ideal for those uses also make them ideal in other situations – for example we have in the past worked with defence companies to develop a Kevlar wrap that is designed to provide a reinforcement section to missile capsules.
At the same time, those properties that make Kevlar ideal for something like a bullet proof vest or a missile casing – that ability to withstand great impact – also makes it the ideal material for creating drum heads! So varied is the right world and I would anticipate that will only become more varied over the coming years as we find a whole range of new applications for this technology.
And does that varied knowledge and experience come in useful when it comes to helping the sales team to identify new opportunities?
Absolutely – I work very closely with Don and the rest of the team in that area to find solutions to the problems that our clients or prospective clients.
And what are you bringing to the table at that stage?
Well obviously the sales team obviously have a phenomenal understanding of composites and their applications – they’ve been working in this industry just as long – and in some cases longer than I have. But on the manufacturing side of the business – we are always developing new techniques and processes and learning more about the materials we are working with so its always really important for us to be involved in those early discussions with clients to really understand the issues they are facing and that really helps us to apply what we’ve learned elsewhere and bring those solutions to the table.
Those lessons could have been learned anywhere from outer Space to the Battlefield so yes we like to think we bring some very unique insight into those conversations.
Click here to find out more and connect with the Advanced Composites team or to discuss your requirements with us in detail